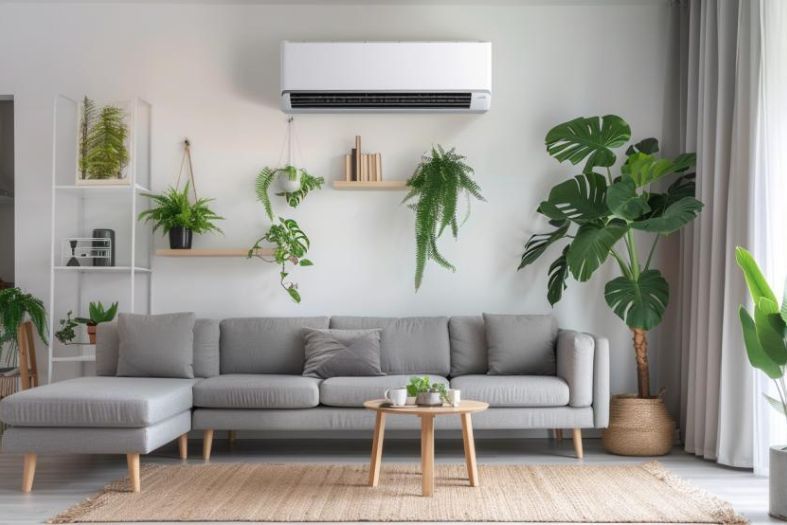
Understanding Mini-Split Error Codes and What They Mean
TL;DR: Understanding mini-split error codes is crucial for maintaining system efficiency and longevity. These codes indicate issues such as high or low pressure, sensor malfunctions, and defrost mode errors. Regular maintenance like cleaning filters and monitoring for debris can prevent many errors. High-pressure errors (E1) often result from dirty coils, while low-pressure errors (E3) can indicate leaks. Sensor malfunctions (F1-F5) require checking or replacing sensors. Defrost mode (H1) and power module errors (H5) usually need professional intervention. For reliable mini-split maintenance and repair, contact Gee Heating and Air in Gainesville.
Navigating the world of mini-split error codes can initially seem daunting. These codes serve as crucial indicators for troubleshooting issues within your system. Understanding mini-split error codes and what they mean is vital not only for maintaining your system’s efficiency and longevity but also for ensuring it operates within its warranty conditions.
This article aims to demystify mini-split error codes, providing a comprehensive troubleshooting guide covering common codes you might encounter. We’ll help you understand that resolving errors is sometimes beyond your capabilities, and that’s when you need to turn to professionals.
Understanding Mini-Split Error Codes
Given the complex electronics that govern the mini-split systems and the use of coolants in their primary performance, errors in these areas are among the most common ones. Of course, there are other errors that you might run into as well, but there’s no need to panic.
Every mini-split code features a letter and a number, indicating which area of the system is underperforming or malfunctioning and categorizing the issue at hand.
Essentially, displaying errors is the system’s way of ensuring you cannot use it while it’s not in its optimal condition, therefore avoiding further serious damage.
High and Low-Pressure Error Codes
These codes are by far the most common ones and have to do with the mini split’s internal pressure system, with the letter “E” indicating that this area needs troubleshooting.
Understanding them is the first step to being able to resolve them:
- E1: This code often appears when the system’s pressure is elevated, usually due to dirty coils or overcharging. Regular inspection of the coils and fans is advised to ensure they’re functioning properly. Given that all components are operating flawlessly, professionals will focus on the high-pressure switch to gauge potential overcharging.
- E3: Indicates low pressure within the system. It’s important to check for dirty filters and coils. If these elements appear clean, a technician should inspect for any leaks.
- E5: This error typically indicates overcurrent protection mode, which gets activated whenever high voltage or unstable low supply voltage is present. A technician’s assessment is required to stabilize the electrical supply.
- E7: Occurs when the indoor and outdoor units are set to different modes, leading to a mode conflict. Ensuring that both units are set to the same mode can often resolve this issue and is usually manageable by the homeowner.
If your system is underperforming, begin by checking the filters and coils. Clean these components thoroughly or replace them if necessary. For coils, ensure they’re free from dirt and debris, which can obstruct airflow and reduce efficiency. Check the outdoor unit’s heat exchanger fin and coil. These parts must be clean, straight, and obstruction-free to allow for optimal airflow. Bend the fins back into place if necessary to ensure optimal operation.
Sensor Malfunctions Codes
Sensor malfunctions are denoted by F-series error codes and include the following options:
- F1: Indoor ambient sensor malfunction;
- F2: Indoor evaporator sensor issues;
- F3: A malfunctioning outdoor ambient sensor;
- F4: Outdoor tube sensor error;
- F5: Discharge sensor malfunction.
After locating the faulty sensor using your system’s manual, check for any visible damage or misalignment. If the sensor has been damaged or keeps misbehaving after cleaning, replace it with a manufacturer-approved part. It might be best to contact professionals.
Defrost Mode / Power Module Protection Error Codes
Keeping the coolants under control is crucial for the successful operation of your mini-split system. The letter “H” demonstrates that a displayed error has something to do with an issue in this specific area:
- H1: Indicates the unit is in defrost mode. If the defrost process is malfunctioning, it may suggest potential trouble with the control sensor or perhaps the heat exchanger.
- H5: This code implies that the intelligent power module (IPM) is in a protective mode of operation to manage voltage and temperature irregularities. This situation necessitates professional service to ensure the compressor functions correctly.
Additional Error Codes
Apart from a general understanding of the letters that refer to specific error categories, there’s no need to go super deep into all the system’s terms. However, you might find understanding the following few additional error codes useful in certain situations:
- C5: Related to jumper issues. Ensure that the jumper is correctly transferred if the control board has been replaced.
- U3: Points to a DC bus bar drop in voltage, requiring professional assessment.
- L9: Signifies activation of power protection mode, likely due to a significant power surge, also necessitates a professional evaluation.
For error codes related to voltage or power issues, ensure that the power supply is stable and within the required range. This can prevent many common electrical issues.
By familiarizing yourself with the most common mini-split error codes, you can better understand potential issues with your system. If issues persist after these checks, or if you’re unsure about your findings, consult a professional. Electrical problems can pose significant risks, and professional assessment ensures your mini-split system runs safely and efficiently.
Preventive Maintenance Tips for Mini-Splits
If you want to avoid common errors in your mini-split system altogether, you should stick to a regular maintenance schedule. While taking care of a mini-split system is pretty straightforward, it can sometimes be tedious. However, wouldn’t you rather go over it regularly as opposed to having to stop using the system until you resolve errors?
Regular maintenance refers to:
Regularly Cleaning Filters
Turn off the system first to guarantee safety. Then, open the cabinet door and gently remove the filters. Depending on the manufacturer’s recommendations, use a soft brush attachment on a vacuum to remove dust or wash the filters with lukewarm water.
Monitoring for Debris and Leaks
Begin by removing any visible obstructions gently using a broom or soft brush. Also, keep an eye out for signs of refrigerant leaks or water around the indoor and outdoor units. Any unusual ice buildup may also point to the presence of a leak.
Scheduling Professional Inspections
Engage a qualified HVAC professional to inspect and perform detailed maintenance annually. Professionals will also check the performance of all mechanical and electrical components.
Sticking to these maintenance tips will help you extend the life of your mini split system, enhance its performance, and ensure it operates error-free throughout the year.
Contact Gee Heating and Air to Resolve Mini-Split Error Codes in Gainsville!
In this article, we’ve discovered that understanding mini-split error codes and what they mean is not just about fixing present issues but about preventing them before they happen.
By adhering to the guidelines for diagnosing, resolving, and maintaining our mini-split systems, we empower ourselves to ensure their efficiency and longevity. This approach not only guarantees our comfort but also safeguards our investment.
If you find yourself in need of expert advice or service to navigate the intricacies of your system’s maintenance and repair, consider reaching out to Gee! Heating and Air for a free estimate and prompt resolution of all your mini-split issues. With the right care and expert support, your mini split system can continue to provide comfort and efficiency for years to come!
Table of Contents
More Articles
Categories
Leave a Reply